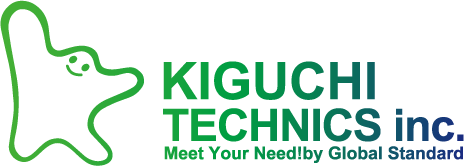
SERVICE
SPECIMEN PREPARATION (METALS)
Specimen Preparation
Continuously innovating and evolving.
Specimen Preparation for Future Generations
The evolution of CAD/CAM systems makes it possible to create NC programs specific to complicated specimen configurations. Some of our customers request machining conditions such as Nadcap AC7101/7 or GEP1TF79. To meet their strict requirements and provide high-quality services, we adopt CAD/CAM systems and prevent human errors.
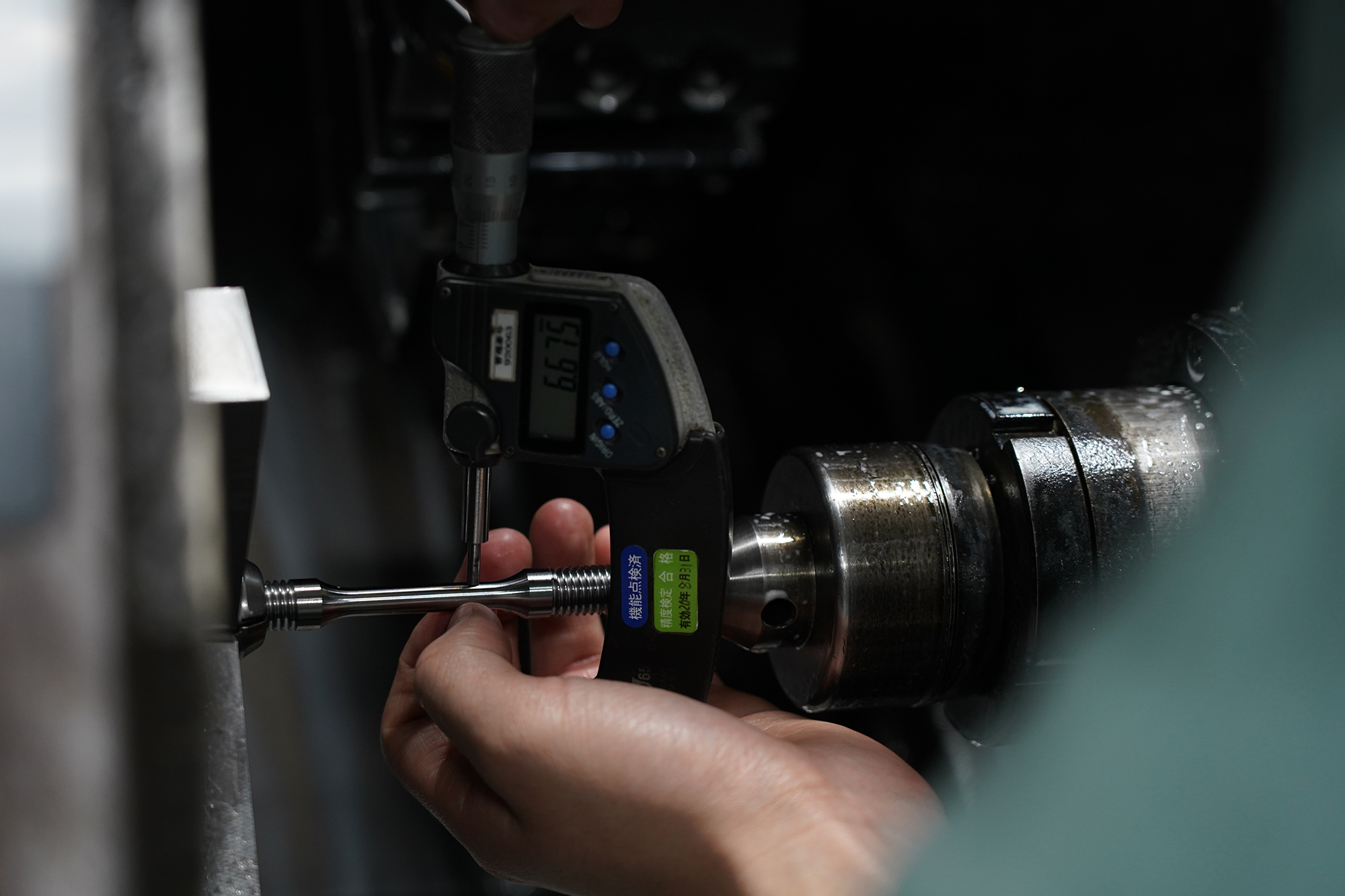
Programming
Solid Modeling
Kiguchi Technics consolidates the internal CAD systems and centrally controls specimen drawings. Those pieces of data have a high degree of compatibility with each other, which allows us to create solid models in a few simple steps.
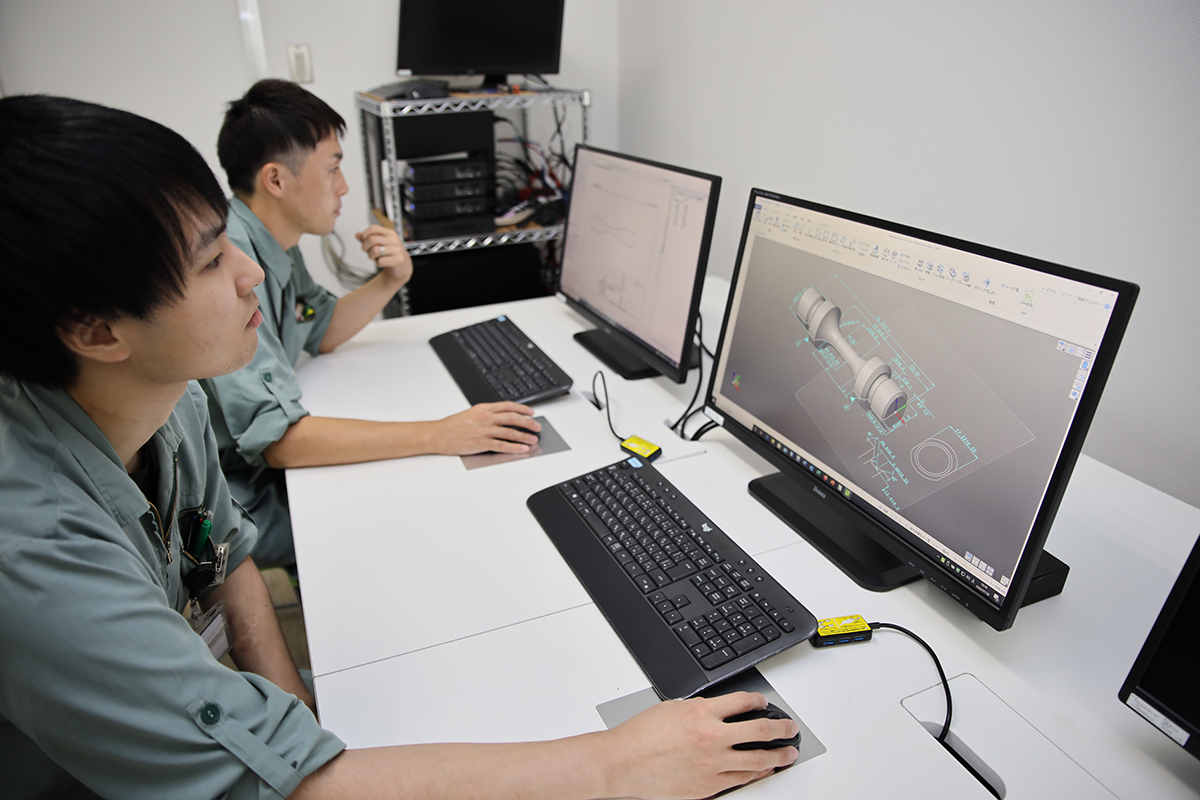
Digitalization of Technologies and Know-how
Kiguchi Technics has received numerous accreditations and approval which require specific technologies and know-how related to specimen preparation. It is important to meet their requirements and we work on building a database to digitalize those technologies and knowledge.
The database usage helps us to automatically create NC programs and simulate a machining process for fast delivery.
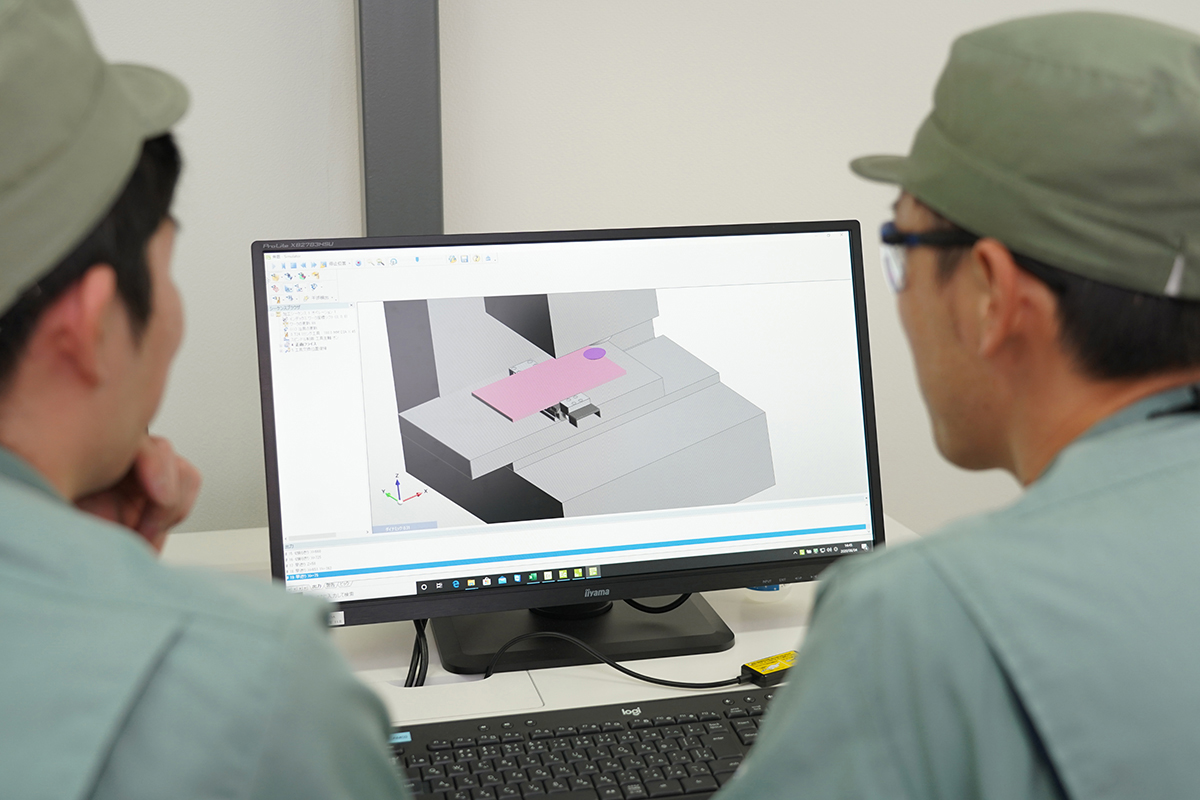
Schedule for Operation
All individual NC machines have a post processor and it is easy for our operators to always check and monitor the operational status of each machine.
This software allows our engineers to transfer NC programs to an operator by using the local networks.
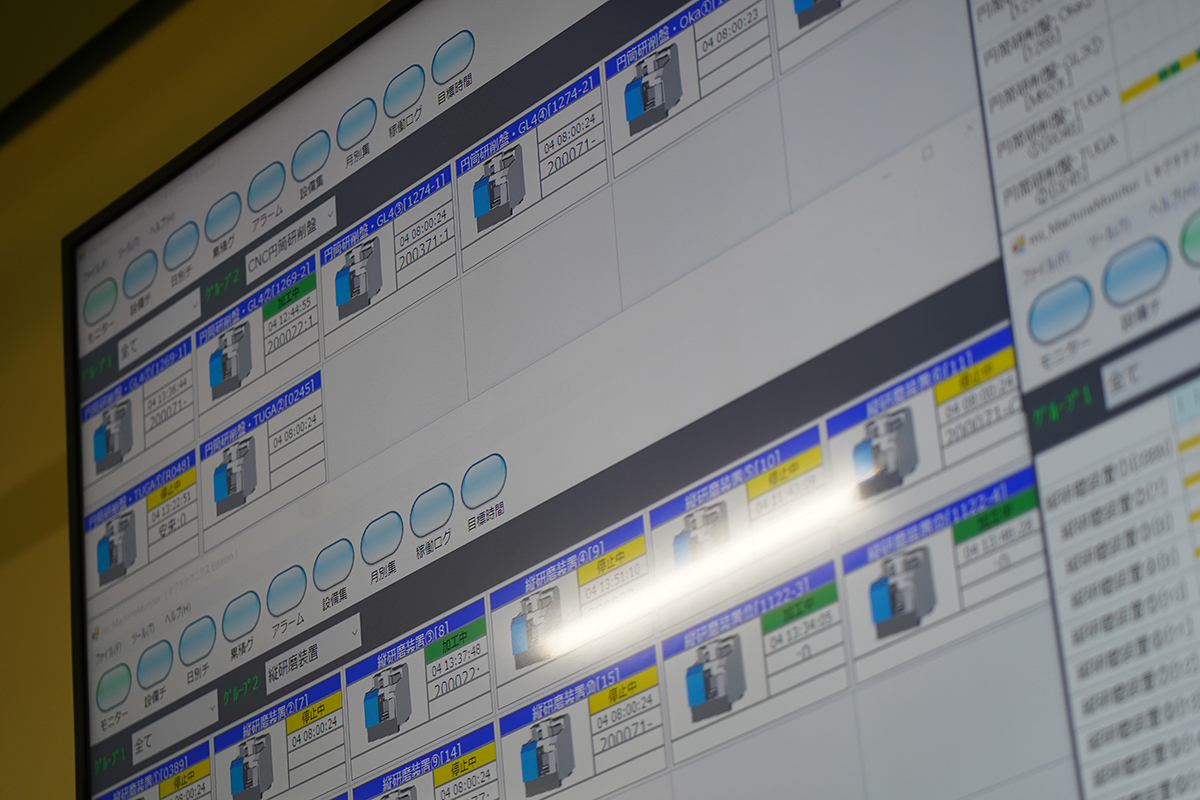
Specimen Machining (NC Lathe)
Combined Lathe
A combined lathe is a machine tool having functions of both NC lathe and machining center.
The evolution of CAD/CAM systems makes it possible to optimize machining processes, realize fast delivery, and maintain a high level of quality.
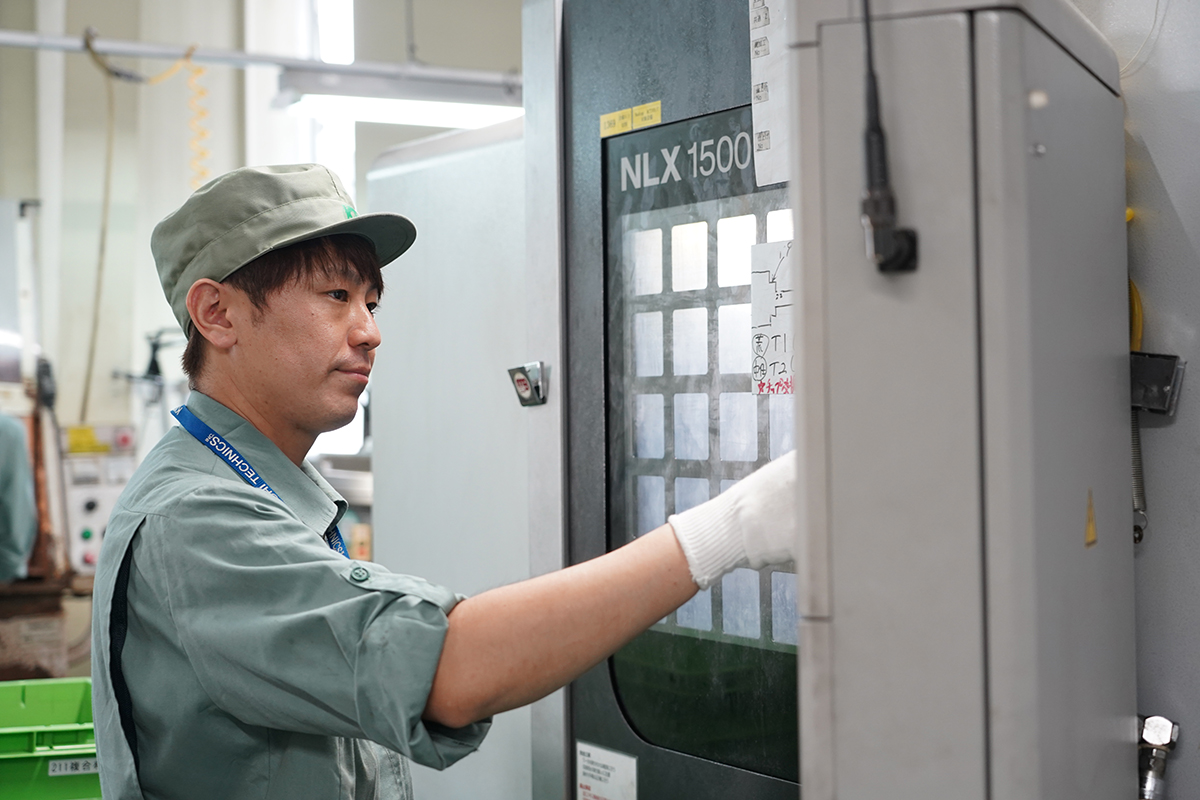
Manual Lathe
Our operators machine specimens from a variety of materials such as square-shaped and deformed materials using a manual lathe. Each person is highly skilled and has a superior ability to use manual lathes.
Specimen Machining (Machining Center)
Machining Center
A machining center is an NC machine tool having a feature of ATC (Automatic Tool Changer) and continuously performs the following processes; boring, milling, hole cutting, tapping, and reaming. Automated services, labor savings, and cost reduction are greatly helped by using this machine.
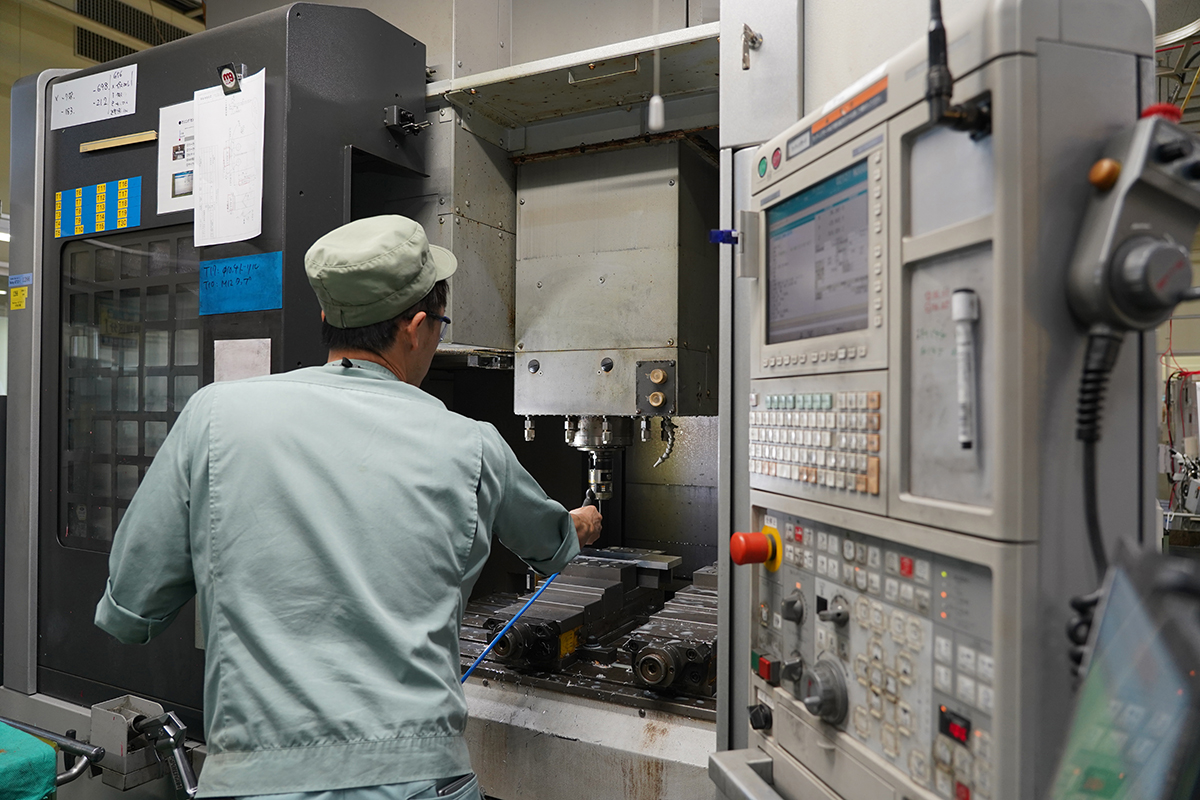
On-machine Measurement
A probe is a small device put inside a spindle of a machining center. Thanks to the introduction of state-of-the-art CAD/CAM systems, we can control the probe within an NC program and provide our customers with a high level of quality in specimen preparation.
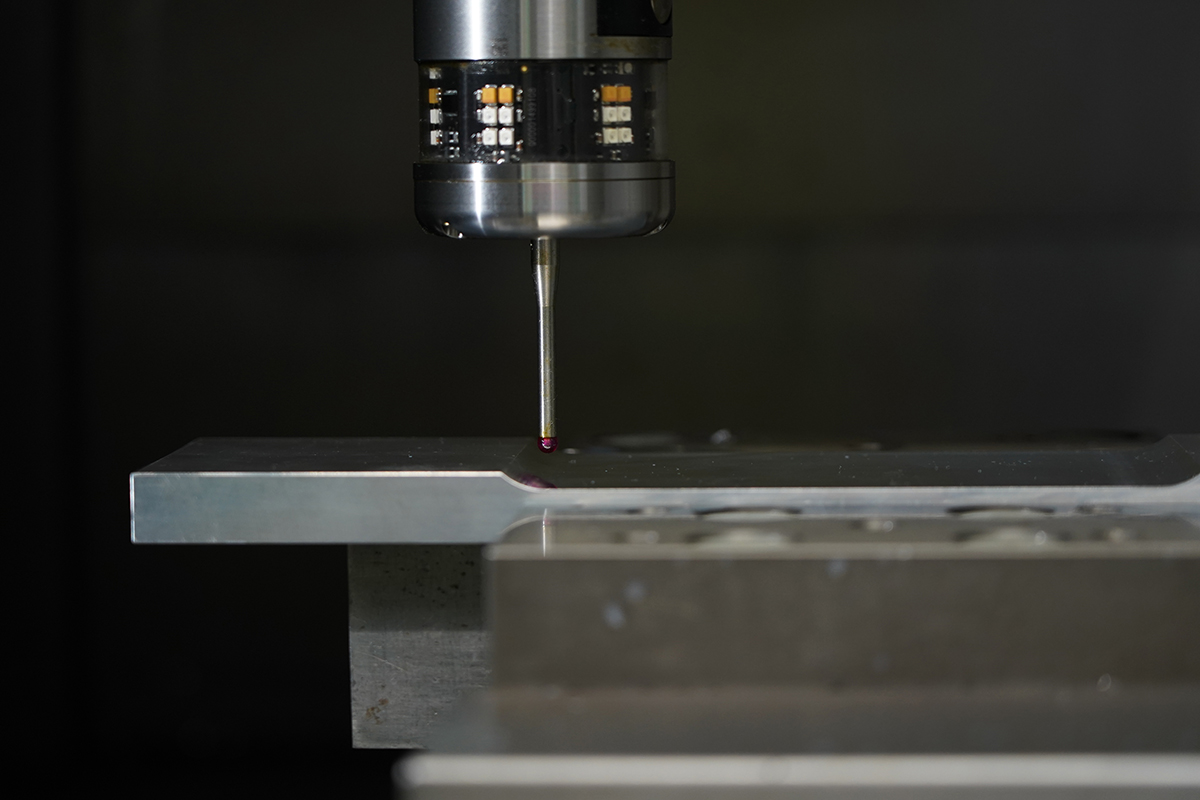
Customized Machines
Machining centers owned by Kiguchi are specially customized to machining processes and supplied materials. Using those machines enables us to machine specimens for various types of specimen configurations.
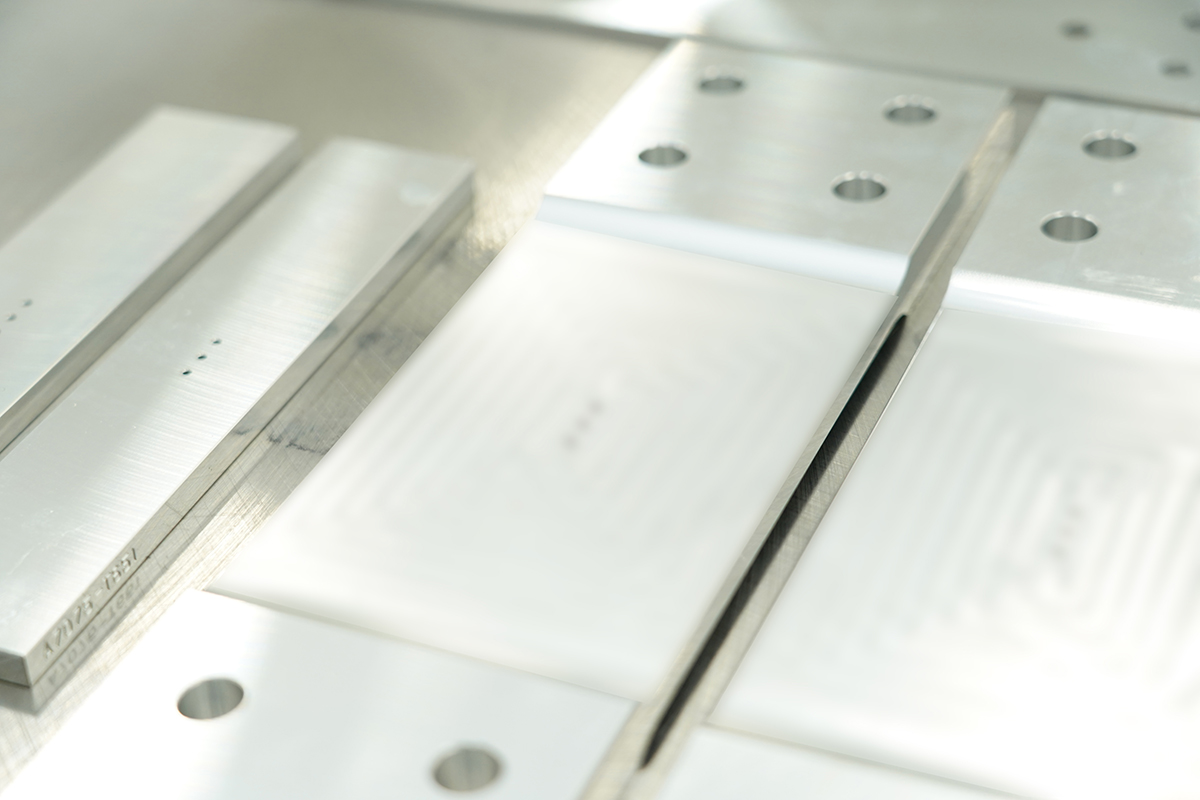
Cylindrical Grinding
Low-Stress Grinding
One of the most important techniques is low-stress grinding to control residual stress on the surface of specimens. Kiguchi Technics owns multiple cylindrical grinders to meet the requirements of numerous accreditations and approval such as Nadcap AC7101/7 (Code Z1, Z2).
Crash Grinding
In general, it is not easy to cut tough, high-hardness, and deformed materials with a blade and also it takes much time for their processes. We introduce a cylindrical grinding machine having large-sized grinding wheels, which enables us to grind such materials. Thanks to the large-sized grinding wheels, automated services and labor savings are realized for fast delivery.
Ultra Precision Micro Profile Grinding Machine
To machine an ultra-precise notch of specimens, Kiguchi Technics owns multiple micro profile grinding machines with a digital microscope. Dressing a grinding wheel by numerical control offers good reproducibility for notch machining.
Surface Grinder
Surface Grinder
Surface grinding is a process to produce a smooth surface finish by using a grinding wheel. The purpose of this process is to achieve appropriate flatness and parallelism and to minimize any factors affecting test results.
Longitudinal Polishing
Automatic Polishing Machine
Kiguchi Technics uses an automatic polishing machine to polish cylindrical specimens. To ensure specimen quality, we comply with Nadcap AC7101/7 (Code Z2), one of the strict requirements for longitudinal polishing processes, and periodically perform surface residual stress measurements by an external agency.
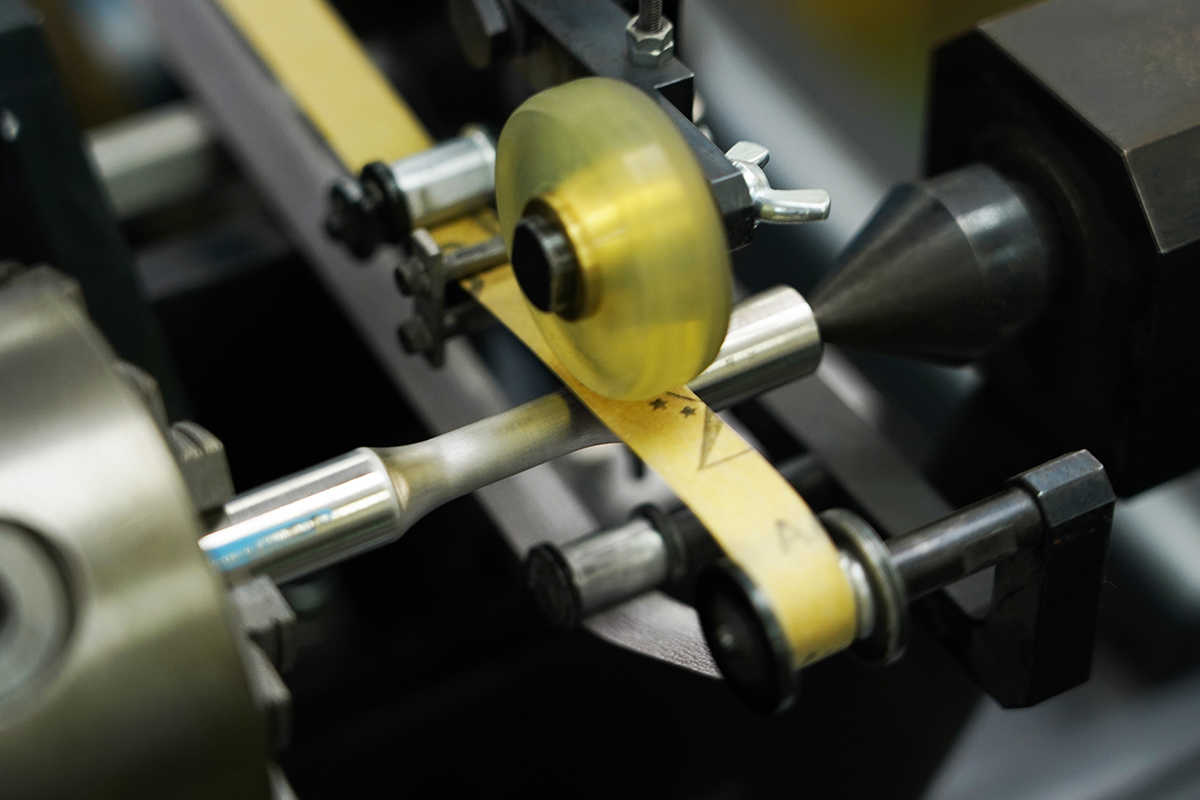
Surface Inspection
For specimens polished longitudinally, visual inspection for specimen gauge sections is carried out at 20X minimum magnification with a microscope. We perform 100% inspection to produce a finished surface without any circumferential defects and undercuts.
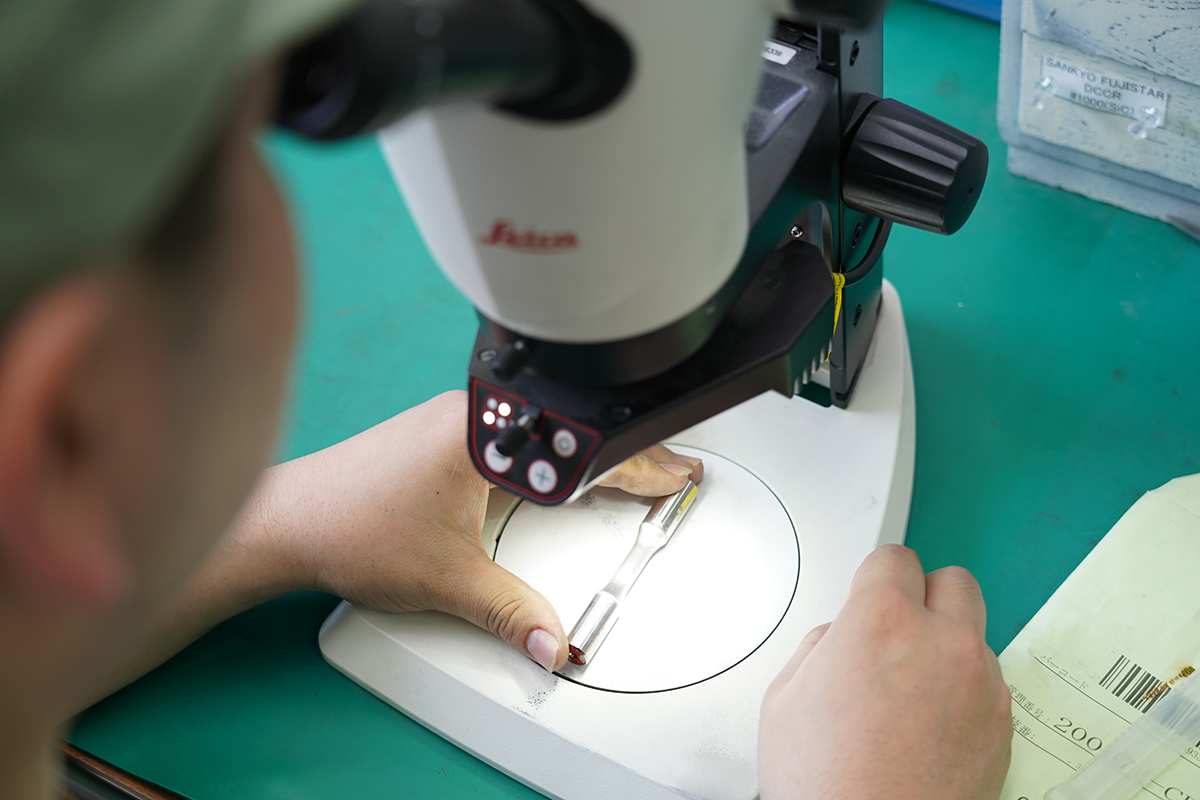
Electrical Discharge Machining
Wire Electrical Discharge Machine (Wire EDM)
To machine large-sized materials, Kiguchi Technics has multiple wire EDMs manufactured by Mitsubishi Electric Mechatronics Engineering Corporation. Work environment temperature control, periodic maintenance by manufacturers, and the usage of large-sized wires enable a long-term operation of the machines.
Die-sinking Electrical Discharge Machining
For machining complicated fixtures and minute artificial defects on the surface of specimens, we own a die-sinking electrical discharge machine manufactured by Mitsubishi Electric Mechatronics Engineering Corporation. The combination of die-sinking and wire EDMs makes it possible for precise electrode design.